
Enclosure Backplates & Panels
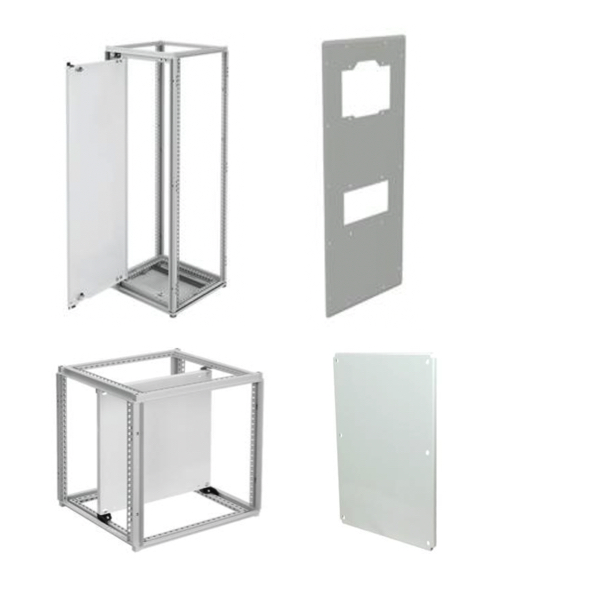
Enclosure backplates and panels are offset from the back of the enclosure allowing electrical devices to be mounted without compromising the integrity or NEMA rating of the enclosure. Most back panels come with pre-cut holes to match the mounting holes in the enclosure. These interior panels can also be removed or replaced, allowing the components to be easily worked on, without uninstalling the entire electrical cabinet. Back panels are made of steel, fiberglass, aluminum, wood, galvanized steel, painted steel, as well as composite materials.
Enclosure gland plates are panels with a gasket. Gland plates provide a removable cable entry and egress, while still maintaining the NEMA rating of the enclosure they are designed for. In some instances, gland plates may be easier to drill or punch than the enclosure wall, and when used properly, may retain NEMA certifications that could be lost if done in the enclosure wall. Gland plates may be used to completely cover cutouts from additions, such as an air conditioner, that are no longer attached, or cover gaps created installing new external equipment that has a smaller connecting footprint.
Subcategories
Products
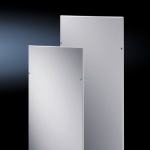
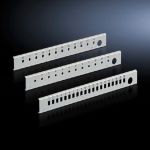
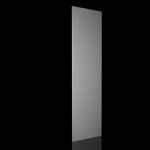
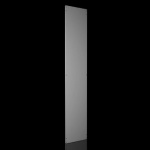
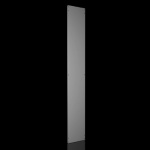
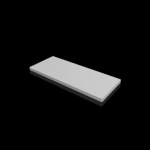
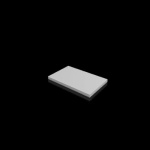
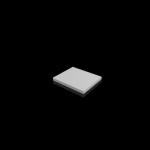
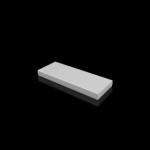
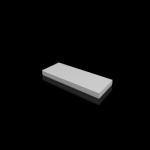

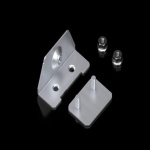
Panel Build Series Part 14: Drilling and Tapping
Drilling and tapping holes into a steel back plane for hardware attachment.
Take inventory of the tools needed for the job.
A metal punch is used to make a small divot in the metal so that the drill bit won't wander, a very sharp machine drill bit and a 10-24 tap. The size of the bit and tap will depend on the type of hardware being used to secure the din rail and wire ducting to the panel.
Punch to create divots on previously marked layout.
Always punch before drilling and make sure that the punch is in the center of the mark.
Drilling into the steel back plane.
Make sure that the drill bit is very sharp, use lubrication to prolong the life of the bit, place the bit into the punched divot and start drilling. Clean up any metal shards when drilling is complete.
Tapping the holes to create threads.
Make sure that the tap is very sharp and lubrication is used when tapping the holes. Do not over torque the tap which can cause it to break. Make sure that the tap goes completely through the hole until it turns easily to ensure that the holes have been properly threaded. Test the threaded holes with a screw. Clean up any metal shards. The back plane is now ready for mounting hardware.