
Explosion Proof Motors
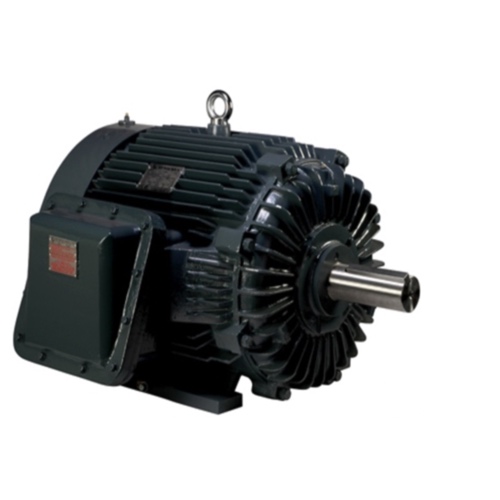
Explosion proof motors are specially designed electric motors that provide safe and reliable operation in hazardous locations where flammable gases, vapors, or dust may be present. These motors are designed to tolerate internal explosions without igniting the surrounding atmosphere, ensuring safety in industries such as oil and gas, chemical processing, and mining. They come in a variety of frame sizes and horsepower ratings, making them suitable for a diverse array of hazardous location applications. Many of these motors are built with totally enclosed fan cooled (TEFC) designs, allowing them to function safely in such demanding environments.
To comply with industry regulations, explosion-proof motors fall into classes and divisions that categorize them according to hazardous substances. Class II motors take care of dust-filled environments, while Class I motors expertly do their job in gas-filled locations. Underwriters Laboratories and various other organizations ensure safety standards for these motors that mandate certain rigorous requirements for operations in locations where hazardous materials are present.
Products
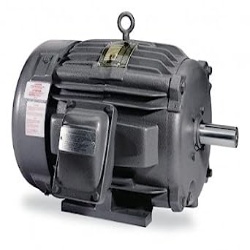
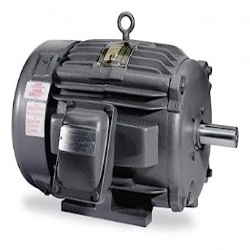
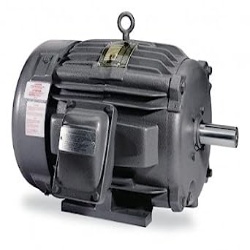
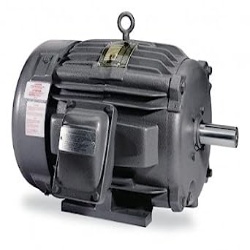
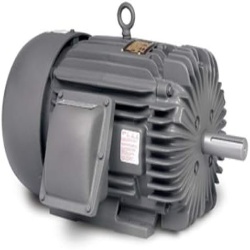
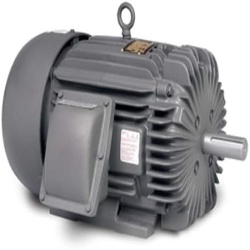
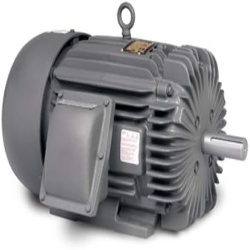
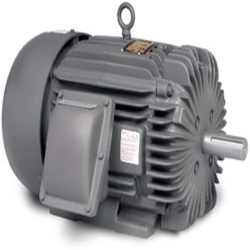
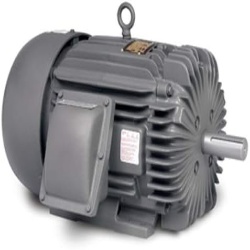
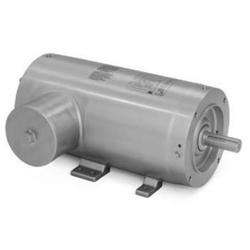
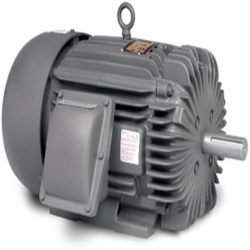
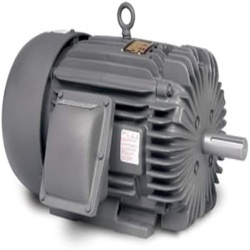
FAQs
What type of explosion protection is needed for motors in explosive dust atmospheres?
Motors in potentially explosive atmospheres require dust ignition-proof (DIP) protection, which ensures that the motor is tightly enclosed to prevent dust ingress and contains any internal ignition sources, preventing ignition of the surrounding dust-laden atmosphere.
Motor Starters, Soft Starters and VFDs
Motor Starters
Motor starters safely start and stop a motor in industrial applications. They are designed with a contactor, overload and circuit protection. They are used when basic motor control is required, where torque on the motor is not a concern and speed control is not needed. The advantages of motor starters include: lower cost, allows for remote operation, allows for monitoring of motor state (with the use of auxiliary contacts) and they are safe and efficient. The disadvantages include: high inrush current that can cause fuses to blow and breakers to trip if the inrush is too high, and the starter will allow a full torque to start the motor which can cause the motor to ramp up to full speed very quickly potentially causing the motor to wear and degrade prematurely.
Soft Starters
Soft starters protect motors from inrush current by gently ramping up the motor to full speed. They provide all of the same functions as a traditional motor starter. The advantages of soft starters include: they are less expensive than a VFD when only startup control is needed, they are a smaller system than a VFD where space is a concern and they prevent unwanted torque upon startup, prolonging the life of the motor. The disadvantages include: they are more expensive than a traditional motor starter and they do not allow for full speed control.
VFDs
A Variable Frequency Drive (VFD) allows for the slow ramp up of a motor during startup and the slowing down of the motor during shutdown. It also allows for full speed control during the entire run cycle of the motor. VFDs provide the same functions as both the traditional motor starters and soft starters. The advantages of VFDs include: full speed control (start, stop and in-between), more custom control and monitoring, energy savings due to efficient motor usage and less wear and tear on the motors. The disadvantages include: they are more expensive and larger than other motor control options and they generate heat that may require fans or AC units.