Phase Converters
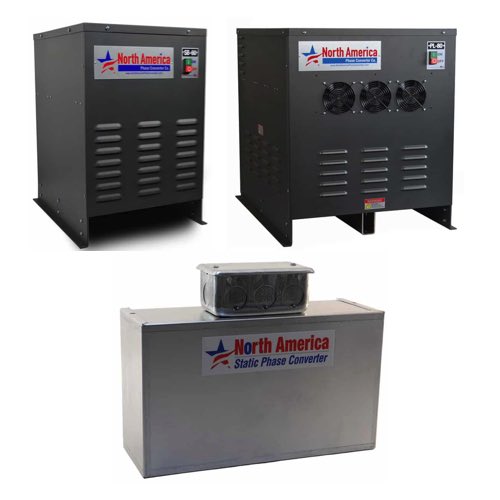
Phase converters are electrical devices used to convert single-phase power into three-phase power, enabling the operation of three-phase machinery in locations where only single-phase power is available. This is particularly useful in rural or residential settings where utility companies often do not supply three-phase service due to infrastructure costs. The three-phase power produced by a phase converter allows equipment like motors, pumps, compressors, and CNC machines to run efficiently and smoothly.
There are several types of phase converters, including rotary, static, and digital. Rotary phase converters use a generator-like motor (idler motor) to create a third voltage leg, producing balanced three-phase power that is suitable for most motor loads and some sensitive electronics. Static converters are simpler and less expensive but only provide true three-phase power during motor startup and drop to single-phase power during operation, making them better suited for light-duty applications. Digital phase converters, on the other hand, use advanced electronics to generate a consistent and balanced third leg of power, making them ideal for high-precision or computer-controlled equipment.
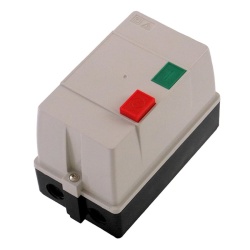
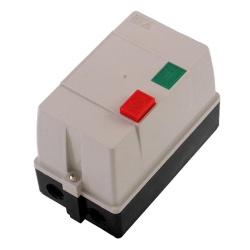
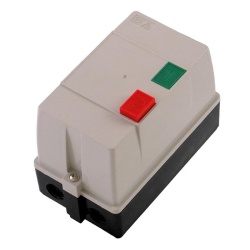
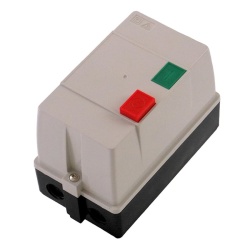
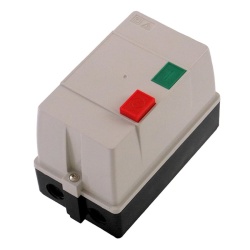
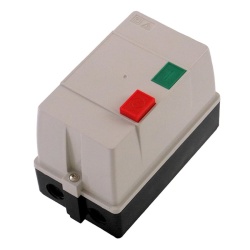
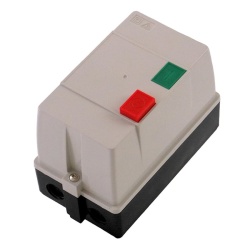
How to Use a Multimeter
Measuring AC Voltage
Set the dial to the AC voltage symbol and plug the red probe into the voltage port. Place the red probe into the hot terminal block and the black probe into the neutral terminal block. Make sure the probes are fully seated to something that can conduct electricity, like the screws on the terminal blocks. The measurement is taken in parallel with the load.
Measuring DC Voltage
Set the dial to the DC voltage symbol and leave the probe in the same port as it was for the AC voltage measurement. Place the red probe to DC positive and the black probe to DC negative. The measurement is taken in parallel with the load.
Measuring Current or Amperage
Set the dial to either milliamps or amps. Move the red probe to the DC amp port. The multimeter is now set to measure DC current. Remove the wire that is sending power to the load and place one probe on one end and the other probe on the other, to complete the circuit, allowing power to bypass the load. The meter will break the circuit and measure the current in series with the voltage source. This allows the meter to measure the current that is going to the load.
Measuring resistance
Make sure that the load is disconnected from the electrical circuit, otherwise, the resistance measurement will not be accurate. Set the dial to the ohm symbol and place the red probe into the voltage port. Place one probe on one conductor and the other probe on the other. Take the reading.
Measuring Continuity
Meter settings stay the same as previous measurements, with the addition of pressing the audible button. Place the probes anywhere on the electrical circuit. An audible tone will sound if there is a continuous, point to point connection. If there is no sound, there is break in the electrical connection, possibly caused by broken or frayed wires.